Understanding Nylon 1
Nylon 1 is a versatile synthetic polymer originally developed in the 1930s. Known for its remarkable durability and flexibility, Nylon 1 has become a staple in various industries. Its chemical composition includes an amide group, which contributes to its high tensile strength and resilience.
Compared to other types of nylon, Nylon 1 stands out due to its unique properties, making it a preferred choice for many applications. Let's delve into what makes Nylon 1 exceptional.
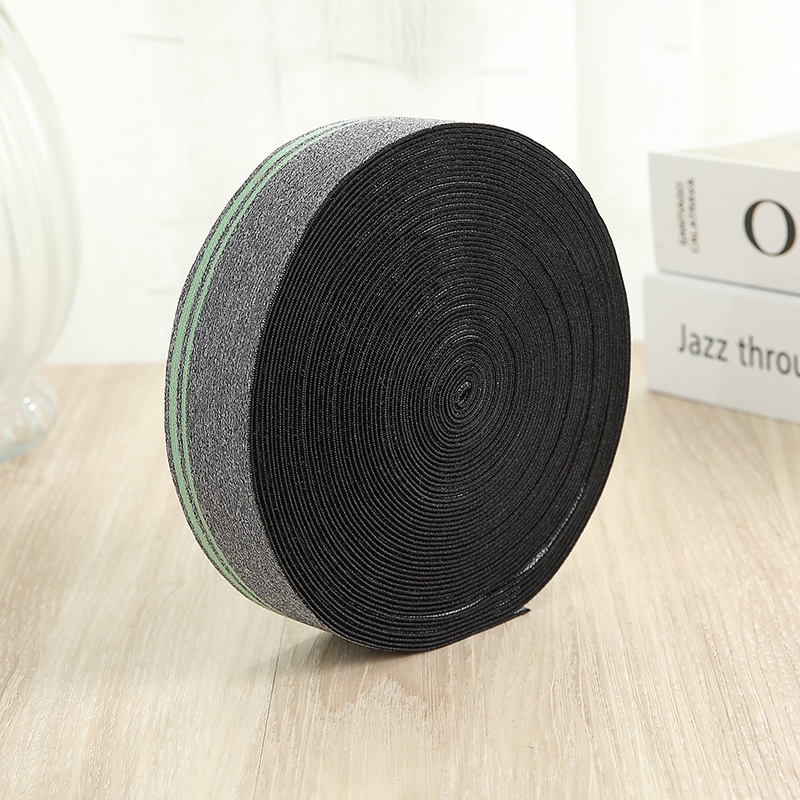
Key Features
High Tensile Strength: Nylon 1 can withstand significant stress and strain, making it ideal for high-load applications.
Excellent Abrasion Resistance: This property ensures that Nylon 1 maintains its integrity even in harsh conditions.
Low Friction Coefficient: Nylon 1's smooth surface reduces friction, which is beneficial for moving parts and mechanical components.
Resistance to Chemicals and Heat: Nylon 1 is resistant to many chemicals and can endure high temperatures, enhancing its suitability for industrial uses.
Common Applications
Textiles and Fabrics
Nylon 1 is widely used in the textile industry for making clothing and outdoor gear due to its durability and resistance to wear and tear.
Industrial Uses
In the industrial sector, Nylon 1 is used to manufacture machinery parts and components, offering longevity and reliability.
Automotive Industry
The automotive industry benefits from Nylon 1 in engine parts and interiors, where it provides strength and heat resistance.
Consumer Products
Nylon 1 is also prevalent in consumer products like kitchen utensils and electronic housings due to its versatility and ease of manufacturing.
Benefits of Using Nylon 1
Durability and Longevity: Products made from Nylon 1 last longer and withstand daily wear and tear.
Cost-Effectiveness: The material's durability translates to cost savings over time.
Versatility: Nylon 1's properties make it suitable for a wide range of applications, from textiles to industrial components.
Ease of Manufacturing: Nylon 1 can be easily molded and extruded, facilitating various manufacturing processes.
Working with Nylon 1
When machining and fabricating Nylon 1, it's essential to use sharp tools and maintain proper cooling to prevent overheating. For molding and extrusion, controlling the temperature and pressure is crucial to achieve the desired shape and finish.
Surface finishing techniques such as polishing and coating can enhance the appearance and performance of Nylon 1 products.
Environmental Impact
Nylon 1 is recyclable, contributing to sustainability efforts. Innovations in eco-friendly nylon production are making this material even more attractive, reducing its environmental footprint compared to other synthetic materials.
Challenges and Considerations
While Nylon 1 offers numerous advantages, it has potential drawbacks such as moisture absorption, which can affect its mechanical properties. Solutions like surface treatments and additives can mitigate these issues.
Handling Nylon 1 requires safety precautions to prevent exposure to harmful chemicals during processing.
Future Trends and Developments
The future of Nylon 1 looks promising, with ongoing advances in nylon technology leading to new applications and markets. Emerging trends include the development of bio-based nylons and enhanced performance materials.
Expert Insights and Testimonials
Industry experts praise Nylon 1 for its versatility and reliability. Case studies highlight its success in various applications, and user feedback underscores its effectiveness in real-world scenarios.
Resources and Further Reading
For more information on Nylon 1, check out recommended books and articles, join online forums and communities, and explore industry reports and whitepapers for in-depth knowledge.
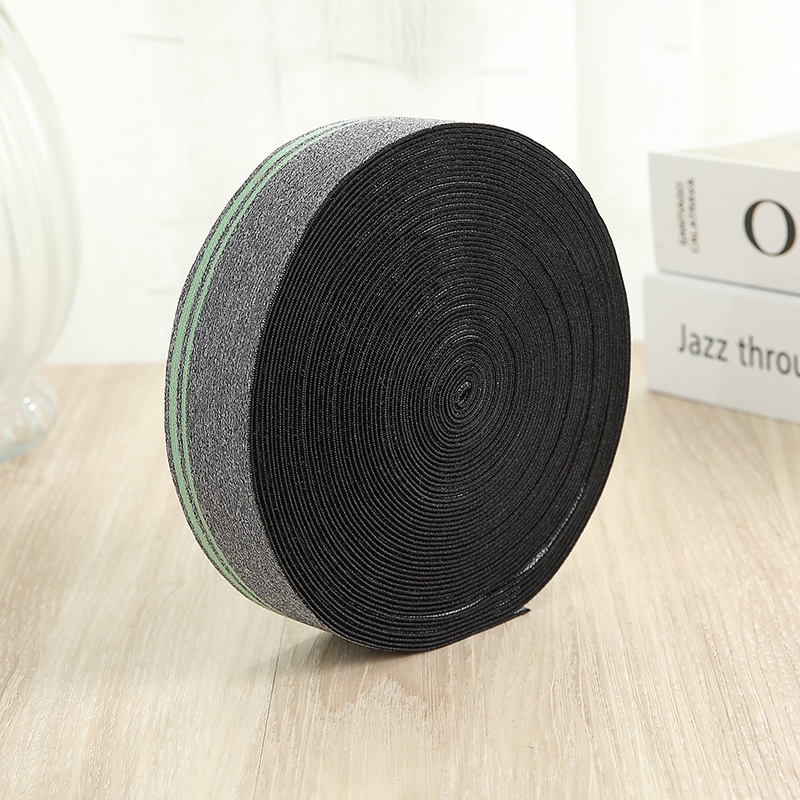