In an era where efficiency and innovation drive every industry, shuttleless technology stands out as a transformative advancement in textile machinery. Understanding its evolution and the unique mechanics of the Shuttleless 12 can offer insights into how this technology has revolutionized traditional weaving methods.
Understanding Shuttleless Technology
The journey of shuttleless technology began several decades ago when engineers sought to improve upon the limitations of conventional shuttle looms. Traditional shuttles, though effective, came with challenges related to speed, maintenance, and filament breakage. The introduction of shuttleless weaving machines offered solutions by eliminating the need for a shuttle, thereby enhancing production rates and reducing mechanical complexity.
The Shuttleless 12 represents the pinnacle of these innovations, integrating state-of-the-art engineering with practical functionality. Unlike its predecessors that relied on bulky mechanisms to process threads, the Shuttleless 12 features streamlined electronics and precision-engineered components that contribute to its superior performance and reliability.
Core Scientific Principles Behind Shuttleless 12
Aerodynamics and fluid dynamics play crucial roles in the efficient operation of the Shuttleless 12. By optimizing airflow management within the machine, it achieves remarkable speed and efficiency improvements. This intricate design minimizes air resistance and maximizes kinetic energy transfer, allowing for faster thread movements and less energy consumption.
Material science also contributes significantly to its advanced capabilities. The use of lightweight composite materials not only ensures durability but also enhances stress resistance. These composites reduce overall machine weight without compromising structural integrity, enabling higher speeds and more precise operations while extending the equipment's operational lifespan.
Engineering Marvels of Shuttleless 12
The Shuttleless 12 boasts an impressive structural design characterized by modular components. This modularity allows for easy assembly, maintenance, and upgrades, making it a versatile choice for various applications. Furthermore, ergonomic considerations have been meticulously addressed, ensuring operator comfort and ease of use.
Precision engineering techniques like CNC machining and laser cutting are employed in manufacturing Shuttleless 12. These technologies ensure exact specifications and flawless construction, resulting in a machine that operates smoothly and accurately. Laser welding further guarantees robust joints, contributing to the overall durability and longevity of the machine.
Operational Mechanics and Functionality
At the heart of Shuttleless 12 lies its powertrain and propulsion systems. Offering both electric and hybrid power options, it caters to a wide range of operational needs. Its design prioritizes energy efficiency, which is reflected in its stellar energy metrics—a feature highly valuable in today’s eco-conscious world.
Advanced control systems drive the automation and intelligent functionalities of Shuttleless 12. Equipped with sophisticated electronics and sensors, it monitors and adjusts its operations in real-time, ensuring optimal performance. The user interface is designed to be intuitive, providing operators with clear information and control over the machine's functions.
Performance Metrics and Testing
Benchmarking against industry standards reveals that Shuttleless 12 excels across multiple parameters, including speed, accuracy, and energy efficiency. Rigorous field tests simulate real-world conditions, proving its capability and resilience under different operating environments. Data collected from these tests drive continuous improvements, ensuring that the machine evolves alongside technological advancements and market demands.
Sustainability and Environmental Impact
Sustainability is a cornerstone of Shuttleless 12’s design philosophy. Eco-friendly material choices and manufacturing processes minimize its environmental footprint. Lifecycle analysis ensures that each stage, from production to recycling, adheres to stringent sustainability criteria. Innovations in recycling and waste reduction further solidify its status as an environmentally responsible choice.
Future Developments and Innovations
The future holds exciting possibilities for Shuttleless 12. Ongoing research and development aim at incorporating even more advanced technologies, such as AI-driven diagnostics and predictive maintenance algorithms. Potential upgrades may include enhanced modular designs for greater customization and interoperability.
Collaborations with leading research institutions and industrial partners will continue to spur innovation, keeping Shuttleless 12 at the forefront of textile machinery technology.
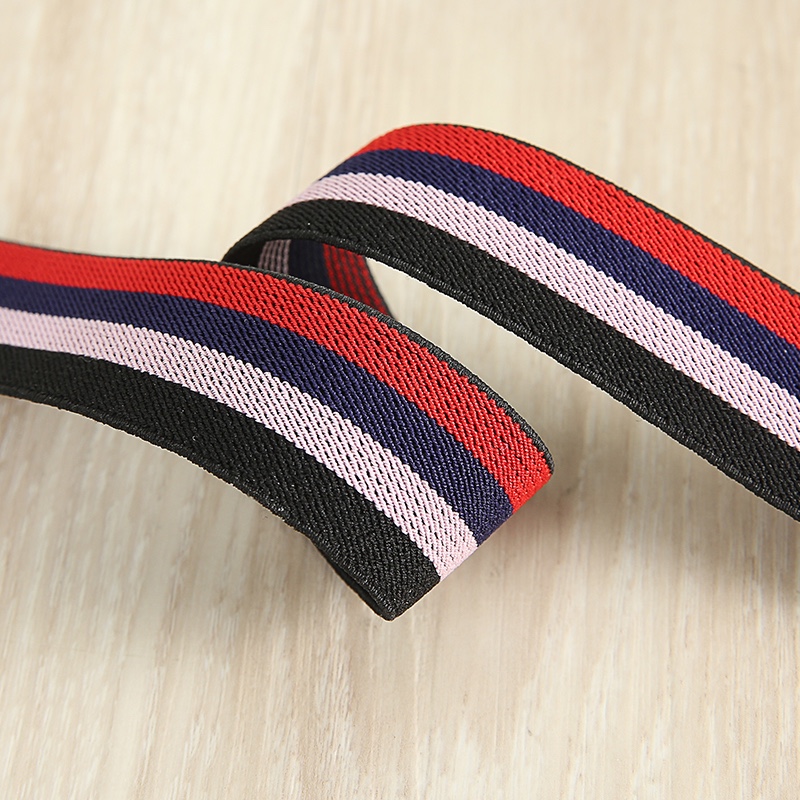
In summary, the Shuttleless 12 embodies the synergy between scientific principles and engineering prowess, delivering unmatched performance and sustainability. As it continues to evolve, it promises to redefine standards and set new benchmarks in the realm of textile machinery.
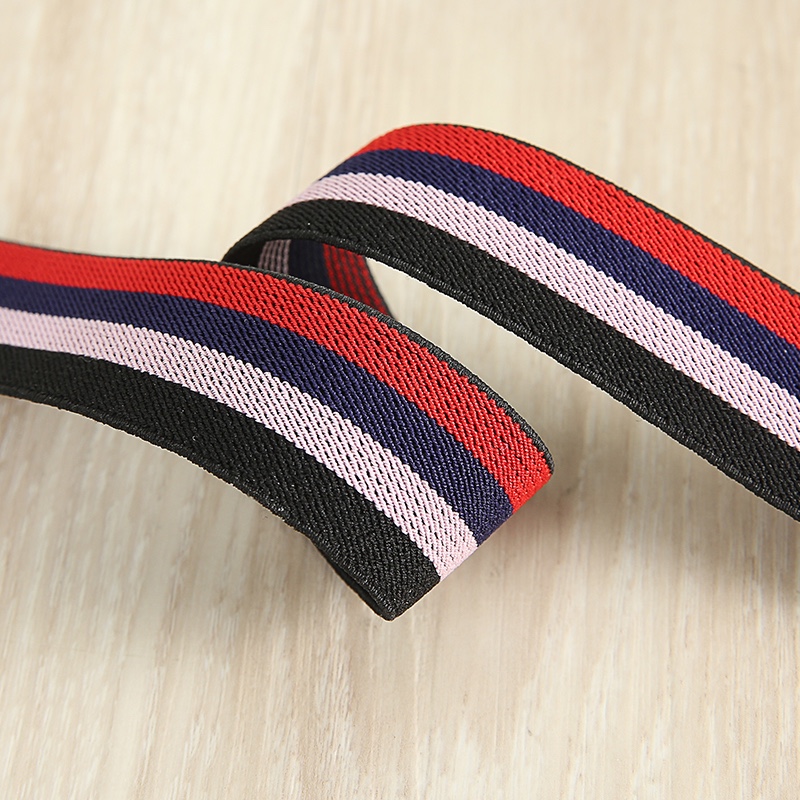