The textile industry, a cornerstone of global manufacturing, is witnessing an unprecedented rise in demand. This surge is propelled by the expanding global population, the fast fashion phenomenon, and burgeoning markets in developing countries. However, the challenge that looms large for manufacturers is to meet this demand without compromising on quality. The quest for achieving a balance between quality and quantity has spurred innovations in textile production technologies.
Textile weaving, a technique with ancient roots, has evolved over millennia. Traditional shuttle looms, known for their simplicity and historical significance, have been the backbone of fabric production. However, these conventional looms are fraught with limitations, including slower production speeds, higher breakage rates, and limited versatility in fabric types they can produce. The inefficiencies inherent in shuttle looms have prompted the search for more advanced weaving technologies.
Enter shuttleless weaving technology. This innovation marks a significant departure from traditional weaving methods, eliminating the need for the shuttle - a component used to insert the weft yarn through the warp. The evolution of shuttleless weaving technology has introduced a plethora of advantages, including higher production speeds, reduced yarn breakage, and the ability to produce a wider range of fabric types.
Zhuo a Ribbon's Shuttleless 12 stands at the forefront of this technological revolution. The Shuttleless 12, a marvel of modern engineering, is designed to address common production bottlenecks, offering unprecedented efficiency and versatility. With its state-of-the-art technical specifications, the Shuttleless 12 ensures seamless operation, minimizing downtime and maximizing output.
The advantages of the Shuttleless 12 are manifold. A detailed analysis of its production efficiency reveals a stark contrast with traditional looms. The Shuttleless 12 not only accelerates production speeds but also enhances fabric quality, offering manufacturers the elusive blend of quality and quantity. This leap in efficiency does not come at the cost of sustainability. The Shuttleless 12 boasts remarkable energy efficiency and a reduced carbon footprint, aligning with the growing emphasis on sustainable manufacturing practices.
The economic and environmental impacts of adopting the Shuttleless 12 are significant. Its energy-efficient operation and lower maintenance requirements present a compelling cost-benefit analysis for manufacturers. By reducing energy consumption and minimizing waste, the Shuttleless 12 offers a sustainable alternative that does not compromise on profitability.
Real-world applications of the Shuttleless 12 paint a picture of success. Textile manufacturers who have embraced this technology report substantial improvements in production efficiency and fabric quality. These success stories underscore the Shuttleless 12's potential to reshape the textile manufacturing landscape, influencing market trends and setting new industry standards.
Transitioning to shuttleless weaving technology, however, is not without its challenges. Manufacturers face hurdles in adopting new technologies, from initial investment costs to training personnel. Despite these challenges, strategies for a smooth transition, including phased implementation and leveraging technical support from Zhuo a Ribbon, can maximize return on investment and ensure long-term success.
The future of textile manufacturing is indelibly linked to the advancement of shuttleless weaving technology. Emerging trends suggest a continued shift towards more efficient, sustainable, and versatile production methods. The Shuttleless 12, with its cutting-edge features and proven success, is poised to play a pivotal role in shaping this future, offering manufacturers a viable solution to the age-old dilemma of balancing quality with quantity.
For manufacturers eager to embark on this transformative journey, getting started with Zhuo a Ribbon's Shuttleless 12 is straightforward. Interested parties are encouraged to reach out for more information on adopting this groundbreaking technology, ensuring they remain competitive in a rapidly evolving global textile market.
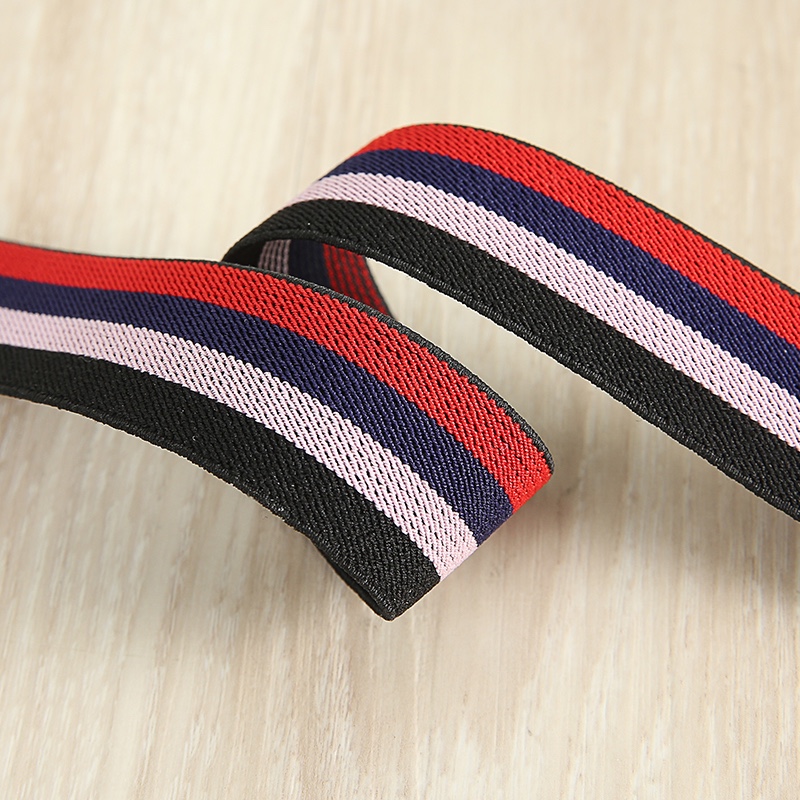